tepcon „instructor“ als Software-Werkzeug gegen Fachkräftemangel
Digitale Anleitungen leisten einen Beitrag zur Bewältigung vielfältiger Herausforderungen im Alltag produzierender Unternehmen. Als Werkerassistenzsystem ist der tepcon instructor auch Teil einer Strategie zum Umgang mit Fragen des Fachkräftemangels.
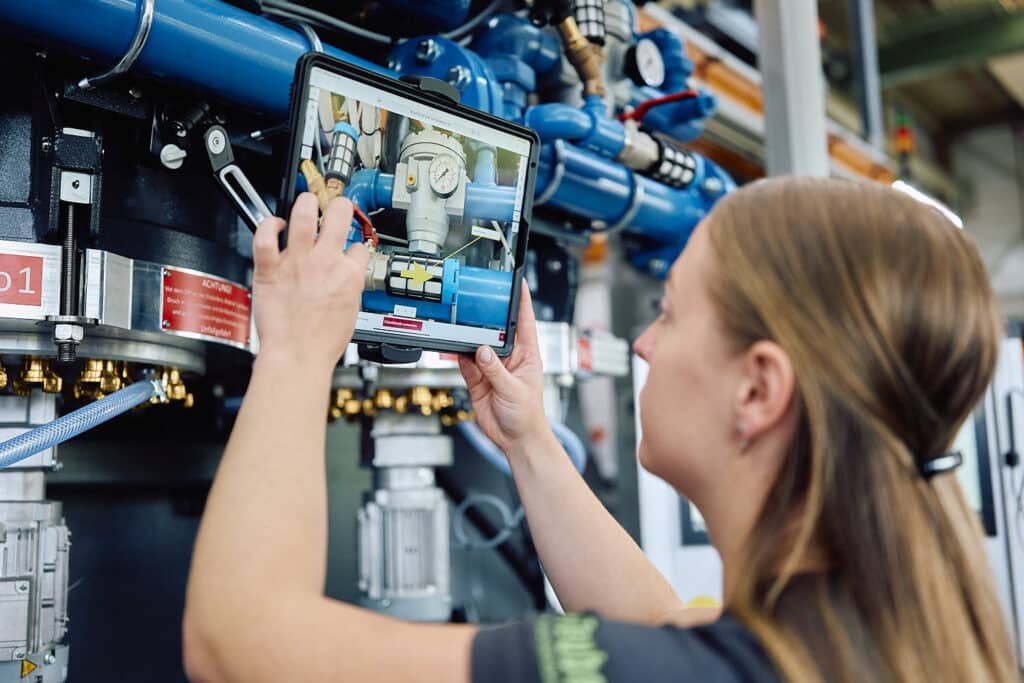
Insbesondere der Mittelstand in den Bereichen der Industrie und verarbeitender Gewerbe steht seit Jahren unter wachsendem Druck. Neben der allgemein angespannten Lage, geprägt von steigenden Strom- und Energiepreisen, schwacher Nachfrage und fehlenden Investitionen, fehlen in fast allen Branchen sowohl qualifizierte Fachkräfte als auch Arbeitskräfte im Allgemeinen. Um sich im wachsenden Wettbewerb behaupten zu können, benötigen Unternehmen Strategien und technische Lösungen, mit deren Hilfe die Effizienz von Produktionsprozessen, bei zumindest gleichbleibender Qualität, gesteigert, Ausfallzeiten reduziert, Instandhaltungskosten gesenkt und gleichzeitig die Einarbeitung und Anleitung selbst unqualifizierter Arbeitskräfte effektiv beschleunigt werden können. Der tepcon instructor, ein System zur einfachen Erstellung digitaler Anleitungen, bietet vielfältige Möglichkeiten, fachliches Know-how in Gestalt von Betriebs-, Montage- und Serviceanleitungen dauerhaft im Unternehmen zu sichern und unkompliziert zugänglich zu machen.
tepcon instructor unterstützt Predictive Maintenance
Experten schätzen den Anteil der Kosten für Wartung und Instandhaltung in der Industrie auf 25 bis 30 Prozent der gesamten Betriebskosten. Ausgaben die sich trotz ihrer Höhe vor allen Dingen durch den Vergleich mit den Kosten durch Ausfallzeiten rechtfertigen. Zeitgemäße Strategien, wie zum Beispiel das Prinzip der Predictive Maintenance – vorbeugende Wartung, zielen deshalb vor allen Dingen darauf ab, diese Ausfallzeiten so kurz wie möglich zu halten und nach Möglichkeit Stillstand komplett zu vermeiden. Voraussetzung hierfür ist jedoch das erforderliche Know-how in allen verbundenen Prozessen. Insbesondere wenn diese nach Möglichkeit mit eigenen personellen Ressourcen abgedeckt und auf externe Dienstleistung aus Kostengründen verzichtet werden soll, müssen alle Aufgaben zuverlässig dokumentiert und für aktuell und zukünftige Verantwortliche verfügbar sein. Der tepcon instructor bietet Unternehmen die Möglichkeit, multimediale Schritt-für-Schritt-Anleitungen zu erstellen. Ohne weitreichende Vorkenntnisse ist es Verantwortlichen damit möglich, einzelne Arbeitsschritte, Handgriffe und die benötigten Werkzeuge in Bildern und Videos zu erfassen, mit Symbolen zu visualisieren und durch zugehörige Dokumente mit weiterführenden Informationen zu verknüpfen. Mittels QR-Codes an Maschinen und Anlagen findet eine einfache Zuordnung der passenden Anleitungen statt, die als browserbasierte Cloud-Lösung mit mobilen Endgeräten direkt vor Ort erstellt und abgerufen werden können.
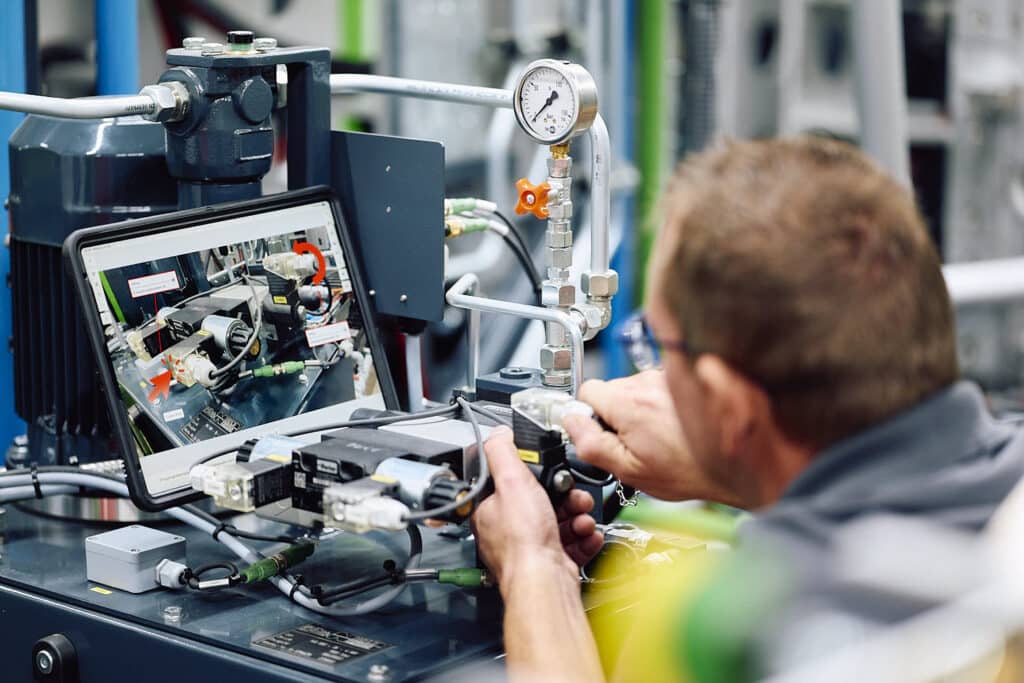
tepcon instructor: die digitale Fachkraft
Der Industrie fehlen in allen Branchen dringend erforderliche Fachkräfte. Darüber hinaus steigt die Fluktuation in Wirtschaftszweigen wie dem Verarbeitenden Gewerbe, Instandhaltung und Reparatur oder im Baugewerbe in den letzten Jahren kontinuierlich. Damit einher geht der Aufwand, den Unternehmen betreiben müssen, um neue Mitarbeiter einzuarbeiten und für die ihnen zugedachten Aufgaben zu qualifizieren. Bei generell angespannten Verhältnissen im Bereich der Personaldichte ist dies eine zusätzliche Belastung. Hinzukommt der generationsbedingt in den nächsten Jahren zu erwartende Wegfall einer großen Zahl an Fachkräften, mit denen Unternehmen nicht nur Arbeitskraft, sondern vor allen Dingen Know-how verlieren, das nicht immer nahtlos auf neu gewonnene Mitarbeitende übertragen werden kann.
Mit Hilfe des tepcon instructor können langjährig erworbene Kenntnisse und Fähigkeiten im Umgang mit Maschinen und Anlagen dauerhaft gesichert werden. Fachkräfte haben ohne zusätzliche Fähigkeiten und mit geringem Aufwand die Möglichkeit, Prozesse detailliert zu dokumentieren und auf Basis individueller Erfahrung Anleitungen zu erstellen, mit deren Hilfe zukünftige Mitarbeiter selbständig Aufgaben übernehmen und erfolgreich bewältigen können.