Inhaltsübersicht
- 1 Effizientes Qualitätsmanagement: So können Sie Ihre Fehlerquote reduzieren
- 2 Das Wichtigste auf einen Blick
- 3 Industrie 4.0 und IoT-Technologien: Treiber der digitalen Transformation
- 4 Sie wollen mehr über die Effizienzsteigerung in der Produktion erfahren?
- 5 Praktische Schritte zur Digitalisierung der Produktion
- 6 Erfolgsfaktoren für die digitale Transformation in der Produktion
- 7 Sie wollen mehr über die Effizienzsteigerung in der Produktion erfahren?
- 8 Nachhaltigkeit und Umweltverträglichkeit in der digitalen Produktion
- 9 Unterstützung bei der Digitalisierung: Institutionen und Angebote
- 10 Auf einen Blick
- 11 Häufig gestellte Fragen
Effizientes Qualitätsmanagement: So können Sie Ihre Fehlerquote reduzieren
Die Herausforderung der Digitalisierung in der Produktion liegt nicht nur im ‘Ob’, sondern vor allem im ‘Wie’. Wie transformiert man traditionelle Abläufe effektiv und kostensparend in digitale Prozesse, und wie stellt man sicher, dass diese nachhaltig zur Wettbewerbsfähigkeit beitragen?
In unserem Artikel navigieren wir Sie durch die Grundlagen, mit denen Sie eine solide digitale Strategie für Ihre Produktionsprozesse entwickeln können – praktische Tipps und erprobte Lösungen inklusive. Denn für den langfristigen Erfolg Ihres Unternehmens ist die digitalisierte Produktion nicht nur hilfreich, sondern sogar unvermeidlich.
Das Wichtigste auf einen Blick
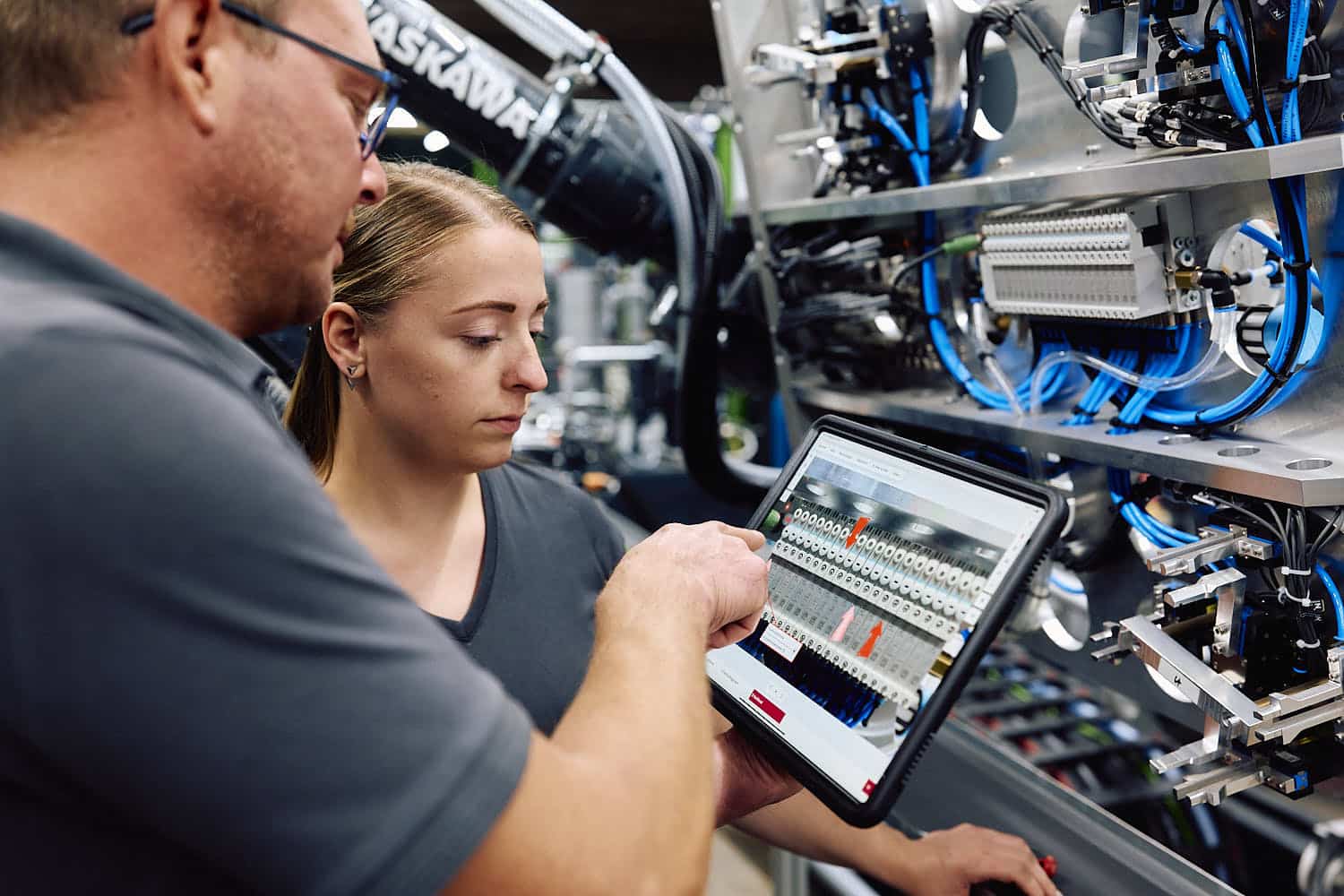
Das Konzept von Industrie 4.0 repräsentiert nicht weniger als die vierte industrielle Revolution. Es führt eine neue Ebene der digitalen Integration ein, die Produktionssysteme agiler und flexibler macht. Vernetzung und Echtzeit-Kommunikation sind die Eckpfeiler dieser Entwicklung, ermöglicht durch fortschrittliche IoT-Technologien.
Diese erlauben eine nie da gewesene Vernetzung von Maschinen und Geräten, sodass zwischen den einzelnen Komponenten eines Fertigungssystems eine effiziente Kommunikation abläuft.
Die dadurch gewonnene Transparenz und die Generierung kritischer Informationen sparen Zeit, schaffen Klarheit und sorgen damit für optimierte Arbeitsabläufe.
Industrie 4.0 und IoT-Technologien: Treiber der digitalen Transformation
Mensch und Maschine kommunizieren im Zeitalter von Industrie 4.0 auf ganz neuen Ebenen. Vernetzte Maschinen und Anlagen, beispielsweise Industrie Smartwatches, sorgen für den schnellen Datenfluss zwischen beiden Parteien. So verkürzt sich etwa die Zeit, die Sie für die Fehlersuche brauchen, wenn die nötigen Informationen jederzeit abrufbar sind. Die Anlage stockt oder es müssen Einstellungen verändert werden? Hier braucht es nicht mehr zwingend die Fachkraft, die vorgibt, was zu tun ist. Digitale Arbeitsanweisungen, wie sie der tepcon instructor ausgibt, ersetzen den menschlichen Anleiter und sind jederzeit verfügbar. So können auch Mitarbeitende, die nicht alle Arbeitsschritte exakt kennen, schnell die nötigen Handgriffe nachschauen, sich Videos oder gar 3-D-Modelle anschauen und anschließend Veränderungen oder Reparaturen Schritt für Schritt ausführen.
Auch Dokumentationsprozesse lassen sich dank der neuen Technologien wunderbar beschleunigen. Daten werden zentral gesammelt und verwaltet, die Nutzer haben jederzeit Zugriff, wenn sie Informationen benötigen.
Mit der fortschreitenden Entwicklung von Technologien sind in den Bereichen Dokumentation und Kommunikation auch in Zukunft noch Optimierungen zu erwarten.
In der Instandhaltung und präventiven Wartung verringern regelmäßige Kontrollen von Maschinen die Ausfallzeiten und erhöhen die Lebensdauer der Anlagen. Auch diese Prozesse lassen sich per digitaler Fernüberwachung verbessern – kostensparend und mit deutlich geringerem Personalaufwand.
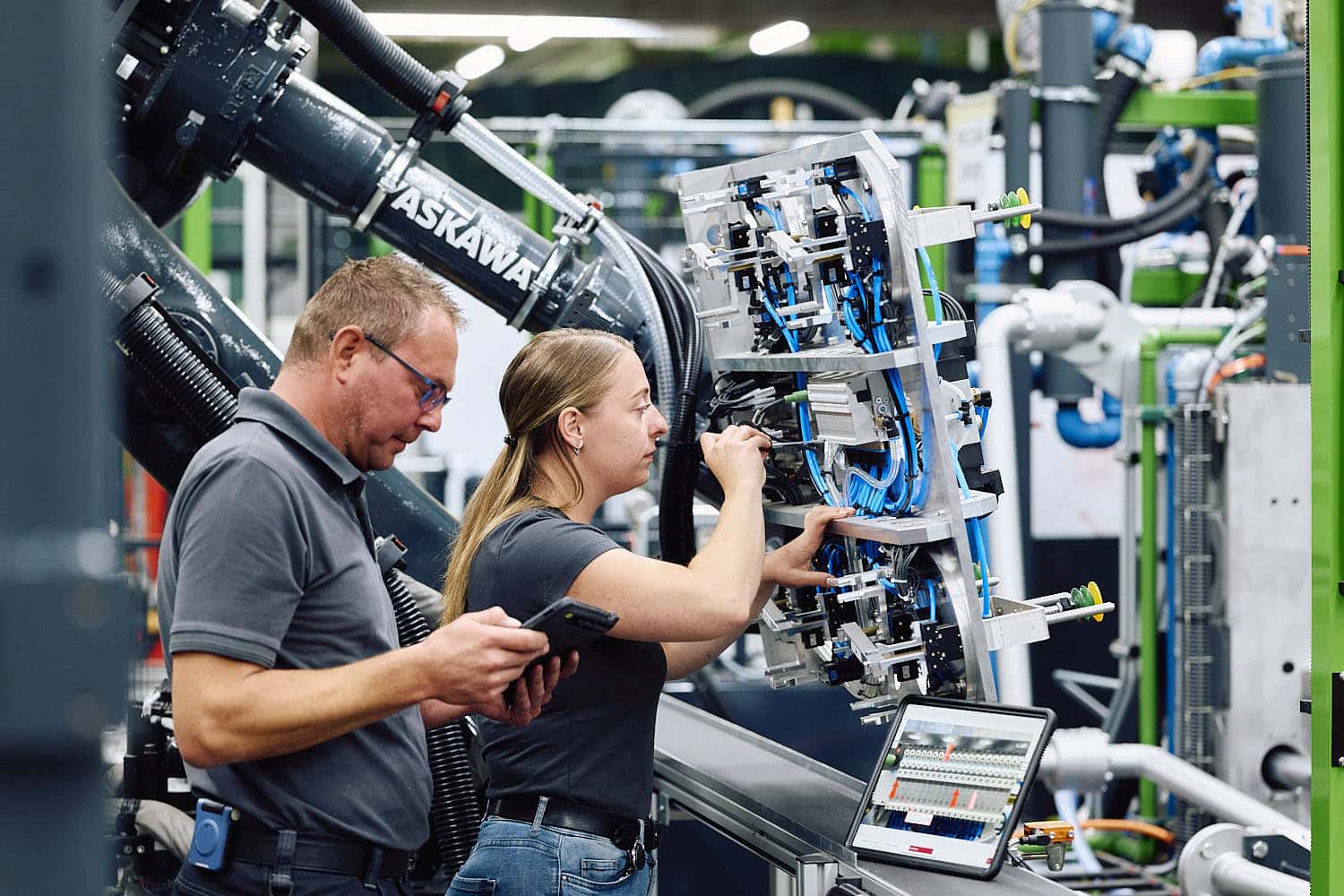
Big Data und Datenanalyse
Die Digitalisierung beschleunigt viele Prozesse, die vorher nur mit Zeit- und Personalaufwand umzusetzen waren. Manche Optimierungen sind überhaupt erst durch die technologische Entwicklung möglich geworden.
Dazu zählt die Datenanalyse, auch bekannt als Big Data. Schneller als jeder Mensch sammelt und analysiert ein Programm unfassbare Datenmengen. Dies ist der Schlüssel zur Aufdeckung von Optimierungspotenzialen in der Produktion, die ohne das digitale Werkzeug gar nicht erkannt würden.
Big Data ermöglicht es, komplexe Datenmengen zu interpretieren und daraus handlungsrelevante Erkenntnisse zu ziehen. So zeigt sich eine detaillierte Einsicht in Produktionsabläufe, und die untersuchten Prozesse können im Ergebnis effizienter gestaltet, an vielen Stellen auch vereinfacht werden.
Darüber hinaus führt die präzise Datendokumentation zu einer schnelleren Identifikation von Fehlerquellen, was wiederum Maschinenstillstände reduziert und die Betriebszeit maximiert.
Die Herausforderung besteht darin, Daten aus einer Vielfalt von Ausrüstungstypen zu normalisieren und zu analysieren, um zu erkennen, welche Daten überhaupt relevant sind und wo sich Erkenntnisse ableiten lassen. Dabei können verschiedene Methoden eingesetzt werden.
Sie wollen mehr über die Effizienzsteigerung in der Produktion erfahren?
Dann beraten wir Sie gerne.
Jetzt anfragenKünstliche Intelligenz und Automatisierung
Die Einführung von Künstlicher Intelligenz (KI) und Automatisierung in Produktionsprozesse führt zu einer beispiellosen Steigerung der Produktivität. KI-Systeme lernen selbständig und passen sich an, sie können immer komplexere Aufgaben ausführen und automatisieren. Das steigert die Effizienz bestimmter Produktionsabschnitte enorm. Auf diese Weise kann etwa die Produktqualität verbessert werden oder Wartungsprozesse können schneller, kürzer und präziser ablaufen.
In der Wartung hilft beispielsweise die KI mit digitalen Zwillingen: Unternehmen wie Caterpillar nutzen diese, um Wartungsbedarf vorherzusagen – präzise Voraussagen machen einen verbesserten Service möglich, was wiederum die Kundenbindung stärkt.
Nicht nur in der Wartung, in allen Bereichen der Produktion zeigt sich: Der Einzug von KI in den Arbeitsalltag bedeutet eine tiefgreifende Veränderung der Fertigungslandschaft. Sie bringt Herausforderungen mit sich, aber schafft vor allem überzeugende neue Möglichkeiten für Innovationen und für die Verbesserung der bestehenden Produktion.
Herausforderungen bei der Umsetzung der digitalen Produktion
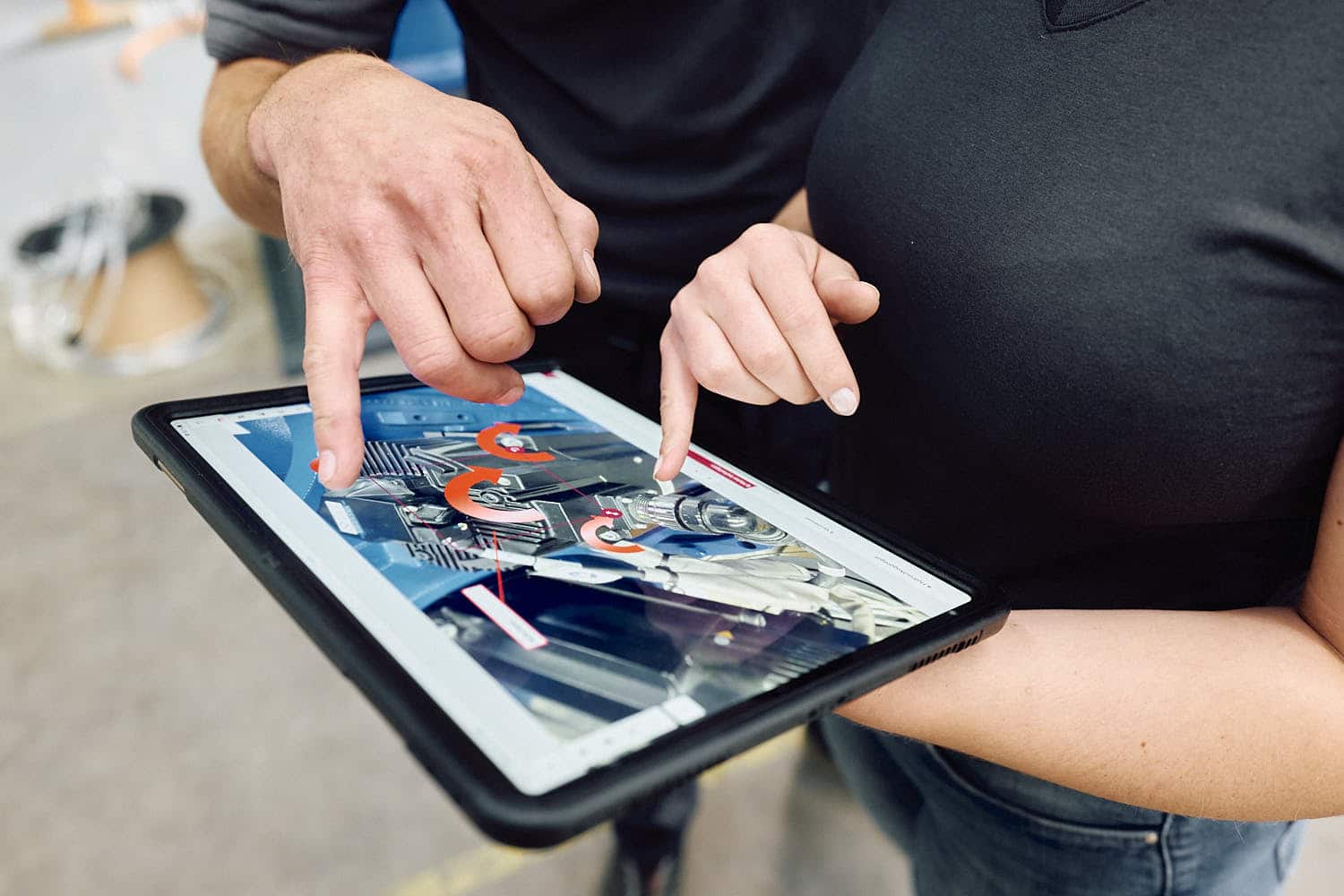
Die digitale Landschaft ist immer in Bewegung und ändert sich schnell – wer sich hier anpassen will, muss in der Lage sein, Innovationen schnell umzusetzen und die aktuelle Entwicklung im Blick haben. Wo diese Innovationsbereitschaft fehlt, da geht nicht nur Optimierungspotenzial verloren – unter Umständen verliert ein Unternehmen so den Anschluss an die fortschrittlichere Konkurrenz.
Die Digitalisierung der Produktion eröffnet zwar zahlreiche Chancen, bringt jedoch auch Herausforderungen mit sich. Zum Beispiel bei der Umstellung auf ein neues System: Die Integration älterer Systeme in moderne Technologien erfordert tiefgreifendes Know-how: Vorhandene Datensätze müsse in das neue System integriert werden, was mitunter aufwändig ist. Das bindet zumindest zeitweise möglicherweise Personal und macht Umschulungen erforderlich.
Beim Umstieg auf die digitalisierte Produktion - oder deren Ausbau - muss auch an betriebsinterne Widerstände gedacht werden. Ein kultureller Widerstand gegen Veränderungen kann die digitale Transformation behindern. Die Bedeutung von Innovationsbereitschaft und der Wille zum Lernen kann hier nicht genug betont werden.
Nicht zuletzt sind Kostenmanagement und ROI-Betrachtungen von großer Bedeutung, da die Vorabkosten für die digitale Umstellung beträchtlich sein können. Gerade in Betrieben, die noch größere Umstellungen vor sich haben, kann der Kostenfaktor als große Hürde erscheinen.
Praktische Schritte zur Digitalisierung der Produktion
Der Weg zur Digitalisierung beginnt mit einer gründlichen Bestandsaufnahme der bestehenden Prozesse: Wo liegt Potenzial brach, an welchen Stellen bringt die Digitalisierung Verbesserungen? Sind die „Baustellen“ identifiziert, folgt die Priorisierung der Prozesse. Dafür stehen verschiedene Tools zur Auswahl: So gibt es Digitalisierungs-Quick-Checks, die bei der Auswahl von optimierungsbedürftigen Prozessen helfen.
Im nächsten Schritt werden Prototypen entwickelt, um die Machbarkeit von digitalen Lösungen in der Praxis zu testen und die Anforderungen für ein Minimum Viable Product (MVP, ein brauchbares Produkt, das mit möglichst geringem Aufwand erstellt wird) zu definieren. Immer wieder wird der Projektplan angepasst, geeignete Technologien werden ausgewählt. Design Thinking kann dabei helfen, ein tiefgehendes Verständnis der Problemstellung zu entwickeln und eine Roadmap mit klaren Zielen zu erstellen.
Es folgt die Realisierungsphase: Der so entwickelte Prototyp wird in den Live-Betrieb überführt.
Erfolgsfaktoren für die digitale Transformation in der Produktion
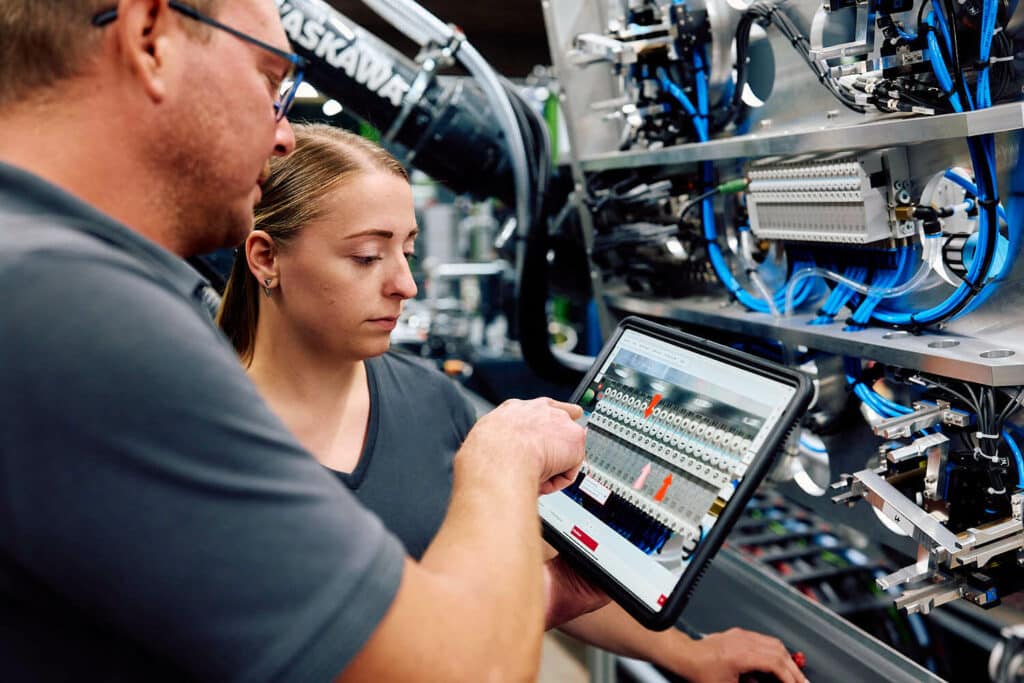
Für eine erfolgreiche digitale Transformation sind verschiedene Erfolgsfaktoren entscheidend.
Grundsätzlich ist die Wandlungsfähigkeit einer Organisation, also die Fähigkeit zu strukturellem und systemischem Wandel, ein wesentlicher Aspekt. Innovationskapazität, welche Kreativität und eine Vision für neue Wege in der digitalen Transformation erfordert, ist ebenfalls von hoher Bedeutung.
Damit der Umstieg gelingt, ist eine ausgeprägte Datenkompetenz nötig: Die braucht es, um relevante Datenquellen zu identifizieren, zu analysieren und zu interpretieren.
Wer mit den schnellen Veränderungen der digitalen Landschaft mithalten will, muss sich fortlaufend weiterbilden - das gilt für alle Ebenen im Unternehmen. Technische und methodische Kompetenz werden immer wichtiger.
Außerdem braucht das Unternehmen Kollaborationsfähigkeit: Wer sich mit anderen Unternehmen und Experten vernetzt, stärkt die eigene Wettbewerbsfähigkeit unter Umständen entscheidend.
Sie wollen mehr über die Effizienzsteigerung in der Produktion erfahren?
Dann beraten wir Sie gerne.
Jetzt anfragenNachhaltigkeit und Umweltverträglichkeit in der digitalen Produktion
Zunehmend wird allen Branchen klar: Nachhaltigkeit und Umweltverträglichkeit sind unvermeidbare Themen im zukunftsfähigen Unternehmen. Nachhaltigkeit ist zu einem zentralen Thema in der Produktionslandschaft geworden und beeinflusst Investitionsentscheidungen. Studien und Schriften wie das Dossier ‘Klimaneutrale Industrie’ bieten Orientierung, wie Unternehmen sich klimaneutral aufstellen können und dabei den steigenden Energiekosten entgegenwirken.
In diesem Zusammenhang sind auch Themen wie die digitale Transformation von großer Bedeutung. Die Nutzung von Cloud Computing und Datenzentren muss unter Berücksichtigung ökologischer Aspekte erfolgen.
Fallbeispiele: Erfolgreiche Umsetzung der digitalen Produktion
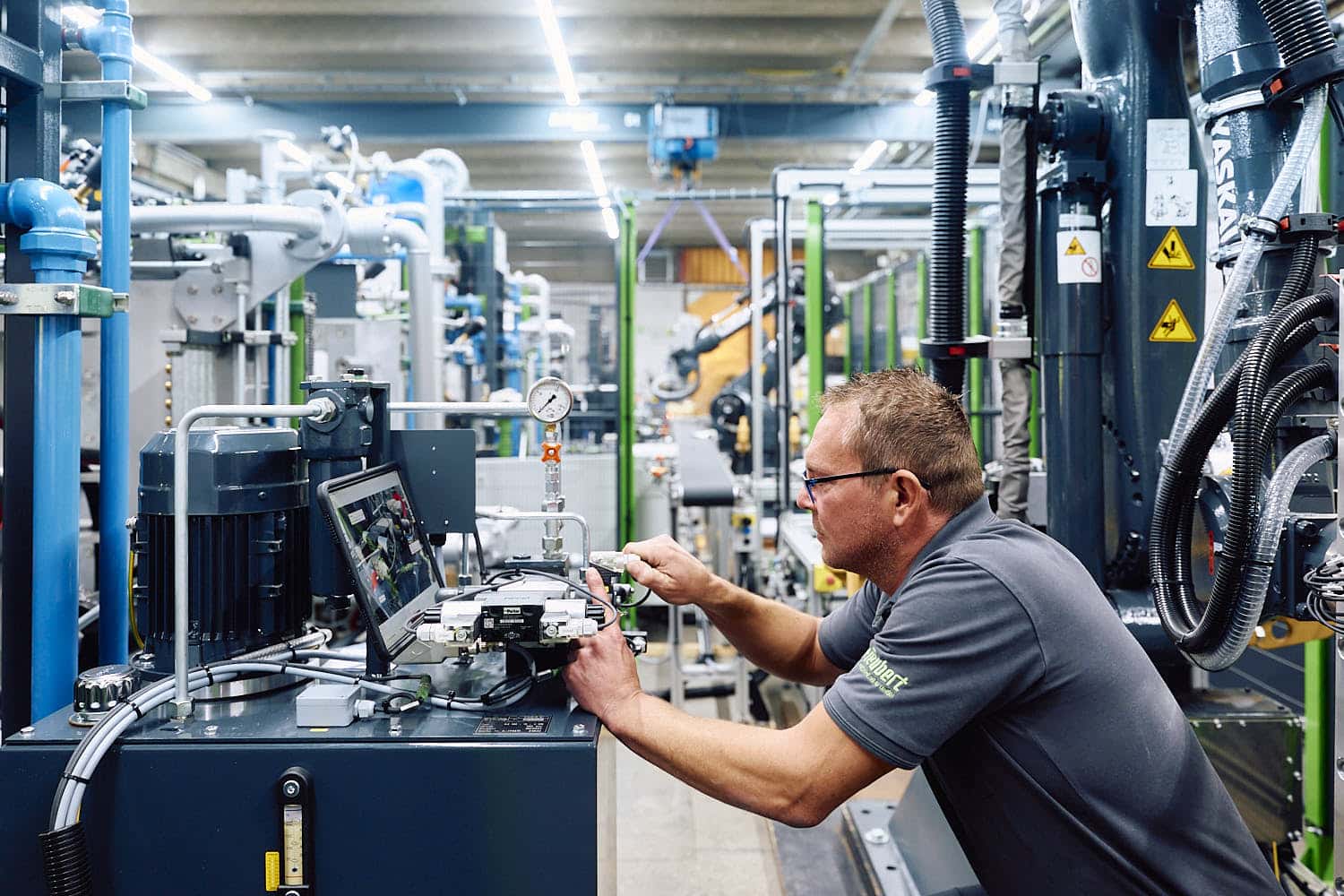
Die praktische Anwendung der Digitalisierung zeigt sich in zahlreichen erfolgreichen Fallbeispielen. Eine Studie hat die Auswirkungen der Prozessdigitalisierung im Anlagen- und Maschinenbau untersucht und festgestellt, dass Unternehmen durch umfassende Digitalisierung ihre Effizienz und Wettbewerbsfähigkeit deutlich steigern konnten.
Die digitalen Anleitungen von tepcon sind ein gutes Beispiel dafür, wie die technologischen Möglichkeiten Zeit und Geld sparen. Hier geht es oft um die Unterstützung von Abläufen bei der Wartung und Instandhaltung. Wo digitale Anleitungen direkt vor Ort verfügbar sind, ist das nötige Wissen jederzeit abrufbar. Zum Beispiel bei der Fehlerbehebung. Früher gab es einen oder zwei Mitarbeitende, die das nötige Wissen haben, wenn bestimmte Fehler oder Wartungsarbeiten anfallen. Dieses Personal muss dann aber auch verfügbar sein. Ein digitales Tool für Arbeitsanweisungen macht die reibungslose Umsetzung jederzeit und durch jeden Berechtigten möglich. Der tepcon „instrucotor“ bietet die nötigen Informationen auf einer bedienerfreundlichen Oberfläche. Er kann über PC, Tablet oder Smartphone abgerufen werden und stellt sofort die nötigen Arbeitsschritte klar und verständlich vor.
Unterstützung bei der Digitalisierung: Institutionen und Angebote
Die Digitalisierung ist eine Herausforderung, die Unternehmen nicht alleine bewältigen müssen. Es gibt zahlreiche Institutionen und Angebote, die praktische Hilfe leisten. Das Bundesministerium für Wirtschaft und Klimaschutz schafft mit dem Förderprogramm ‘Digital Jetzt’ finanzielle Anreize für KMUs, um in digitale Technologien und die Weiterbildung von Mitarbeitern zu investieren.
Mittelstand-Digital Zentren und Fraunhofer-Institute wie IGCV und SCS bieten Unterstützung in Form von Beratung, praktischen Demonstrationen und Weiterbildungsprogrammen, die Unternehmen helfen, die digitale Transformation effektiv umzusetzen.
Auf einen Blick
Die Digitalisierung der Produktion eröffnet ein Universum an Möglichkeiten, um Effizienz zu steigern, Kosten zu senken und die Produktivität nachhaltig zu erhöhen. In der modernen Industrie 4.0 sind Big Data und IoT-Technologien für wettbewerbsfähige Unternehmen zur Selbstverständlichkeit geworden, zunehmend nehmen sie auch das Thema Nachhaltigkeit in den Blick.
Die vorgestellten Fallbeispiele und Unterstützungsangebote sollten Mut machen, diesen Weg zu gehen. Es ist klar, dass die digitale Transformation kein Selbstläufer ist, aber mit der richtigen Strategie und den passenden Ressourcen sind die Hürden überwindbar.
Sie wollen wissen, wie unsere Software-Lösung „instructor“ das Leben und die Arbeit unserer Kunden verbessert? Auch das ist digitalisierte Produktion mit echten, messbaren Ergebnissen in kürzester Zeit – fragen Sie uns, wir beraten Sie gern und stellen Ihnen Beispiele verschiedenster Branchen vor.
Häufig gestellte Fragen
Typische Beispiele für digitalisierte Abläufe im Unternehmen gibt es zum Beispiel im Marketing oder bei der Kundenbindung: Dort haben etwa Chats mit Kunden eine immer größere Bedeutung. In der internen Kommunikation und bei der Dokumentation sparen digitale Tools Zeit und Personal ein. Sie erleichtern das Aufgabenmanagement, gestalten die gesamte Produktion, Logistik und allgemein interne Abläufe deutlich effizienter.
Der tepcon „instructor“, von uns auch gern als digitale Fachkraft bezeichnet, optimiert Arbeitsabläufe, zum Beispiel bei Wartungs- und Instandhaltungsarbeiten, und er übersetzt die Anleitung bei Bedarf auch in verschiedene Sprachen.
Kurz gesagt: Die digitalisierte Produktion ist effizient, günstig und produktiver. Außerdem lässt sich mit geringeren Kosten und weniger Personalaufwand trotzdem auf individualisierte Produkte umstellen, was die Angebotspalette erweitert und so neue Kunden anzieht.
Die Industrie 4.0 setzt auf IoT-Technologien, Big Data, Datenanalyse, Künstliche Intelligenz und Automatisierung, um Produktionsabläufe zu optimieren.
Die Umstellung macht es nötig, ältere Systeme zu integrieren. Sie erfordert zunächst einmal einen gewissen Aufwand von Zeit und Geld. Außerdem braucht es eine gewisse Anpassungsfähigkeit, Lernbereitschaft und Flexibilität im Team, damit sich alle auf die neue Produktionsweise umstellen können.
Um die Digitalisierung ihrer Produktion praktisch umzusetzen, sollten Unternehmen mit einer Bestandsaufnahme beginnen, Prozesse priorisieren, Prototypen entwickeln, diese realisieren und schließlich in den Live-Betrieb implementieren, immer unter Einbezug von Design Thinking und einer klaren Zieldefinition.